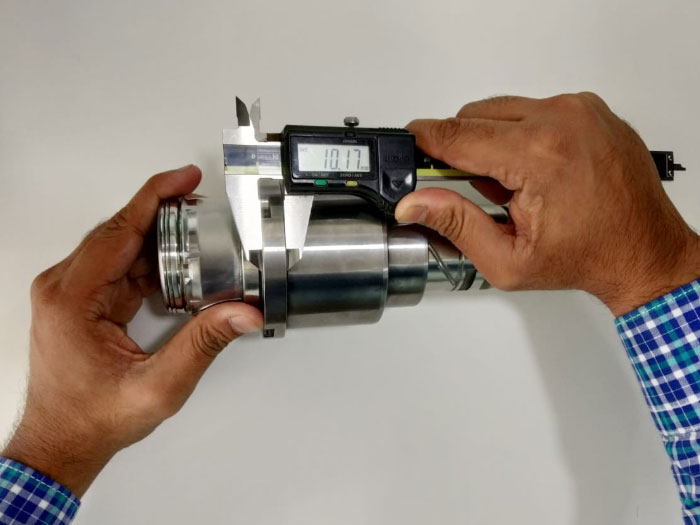
We are able to make all kind of beverage, water and edible oil caps with best quality because of our continuous technological research and all our past experiences. Before turning on the computer and drawing line we simply aim at knowing deeply our customer’s exigencies, understanding what he wants, checking each aspect, going beyond the mere project to create something unique and absolutely suited the new need. The difference our way of working makes is the same as you get the readymade dress from shop and the one which you made from tailor as per your requirement.
For This We Follow The Step By Step Procedure:
First we understand the exact requirement of our customer. For that we take references of their sketches, dummy models, products which need closures etc. We also understand what functionally are the most important point in that product i.e. the shape, the type of threads, the type of problems , the fitment with another meeting product etc.
After this we do the product designing considering all above points and make 2D drawings as well as 3D models.
While doing the engineering drawings as well as 3D models we also consider in mind that the product should be feasible to make the fitment as well as 0% leakage should be there. Also checking the feasibility of caps holding chucks for the high speed and long run machines.
After the approval of the cap design with proper fitment of the product we generally make the Rapid proto type for the same. With the help of this Rapid proto type product we gets the ideas for the various fitments and dimensions.
After getting approval from customer, we start the process of mold making.
After complitetion of production tools we take samples and started inspection of its shape size, checking the fitments, trials for leakage with different pressure. After success we start bulk production.


Aglo has the engineering know-how, capability and proven design standards to transform customer needs into a superior product.
Aglo Tool Crafts in Pursuit of excellence begins right at the design stage with DFMEA, Mould Design reviews, New product design by which we ensure an optimal design for the mould in terms of size, cycle time and maintenance. All this reflects on higher up time of the mould by which high productivity is assured.
STRENGTHS & MERITS:
First we understand the exact requirement of our customer. For that we take references of their sketches, dummy models, products which need closures etc. We also understand what functionally are the most important point in that product i.e. the shape, the type of threads, the type of problems , the fitment with another meeting product etc.
SolidWorks, and AutoCAD.
Solid Models-STEP, IGES, PARASOLIDS.
Design for Manufacturability (DFM) – Value addition in terms of Product Design and Optimum Cycle Times.
Capability to align to customer standards and customization requirements.
After complitetion of production tools we take samples and started inspection of its shape size, checking the fitments, trials for leakage with different pressure. After success we start bulk production.
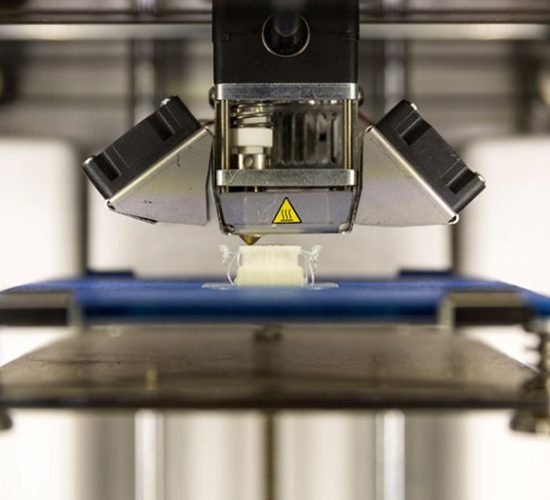